The Evolution of Cleveron 403 Latest Version: Engineering Excellence Redefined
We are launching an upgraded version of Cleveron 403, focusing on improving the configuration for better space optimisation and redefining the future of retail technology and click-and-collect services.
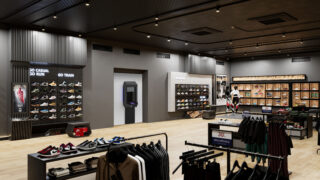